Bullet Train Project: MR Ashwini Vaishnaw inspected under construction tunnel between BKC-Shilphata
Construction of 21 km Long Tunnel including India’s First 7 km Long Undersea Tunnel in the State of Maharashtra for the Bullet Train Project
Mumbai: Minister for Railways #AshwiniVaishnaw inspected a 21 km long India’s first underground/undersea tunnel is under construction between Mumbai bullet train underground station at Bandra-Kurla Complex (#BKC) and #Shilphata in the State of #Maharashtra on Saturday, 18th January, 2025.
Out of 21 km of tunnelling works, 16 km is through Tunnel Boring Machines (#TBM) and remaining 5 km is through #NATM. This also includes 7 km of undersea tunnel at Thane creek.
Construction work has already begun at following locations:
- ADIT (Additionally Driven Intermediate Tunnel) Portal: A 394-meter-long #ADIT tunnel is already completed in May 2024 (record time to 6 months). This has facilitated two additional NATM faces for the excavation work in addition to Shilphata. Due to this additional access. 1,111 meters (622 meter towards BKC/N1TM out of 1562 m and 489 meters towards Ahmedabad/N2TA out of 1628 m) of tunneling work has been achieved.
- The ADIT of dimension, 11-meter X 6.4 meter will give direct vehicular access to the main tunnel during construction and operations and may also be used for the purpose of evacuation process in emergency situation.
- Shaft-1 at Mumbai #HSR station construction site: Shaft depth of 36 meters, excavation work is currently underway.
- Shaft-2 in Vikhroli: Shaft depth of 56 meters is completed. This shaft will be used to lower two tunnel boring machines in two different directions, one towards BKC and another one towards Ahmedabad.
- Shaft-3 in Savli (near Ghansoli): Shaft depth of 39 meters has been completed.
- Tunnel portal at Shilphata: This is the NATM end of the tunnel. Portal work is already completed and 602 meter of tunnel work out of 1628m (N3TM) has been achieved so far.
Precautions being taken during tunnel excavation works
- Sufficient ventilation is being ensured inside the tunnel, ensuring safe and ventilated workforce inside the tunnel sites
- All excavated material is being disposed as per the state governments direction
- Structure/Buildings around the tunnel sites are continuously monitored
- Various types of Geotechnical Instruments like Inclinometers, Vibration monitors, Ground settlement markers, Tilt meter etc. have been installed at and around construction sites for monitoring tilt, settlement, vibration, cracks and deformation. These instruments play a crucial role in making sure that neither there is any risk to ongoing underground works like excavation and tunneling nor to the structures surrounding the site.
Casting yard for tunnel lining:
A dedicated casting yard for casting tunnel lining for the 16 km TBM portion is already operational in Mahape. 77,000 segments will be cast to form 7,700 rings. Special ring segments are being cast for the tunnel lining, each ring comprising nine curved segments and one key segment, with each segment being 2 meters wide and 0.5 meters (500 mm) thick.
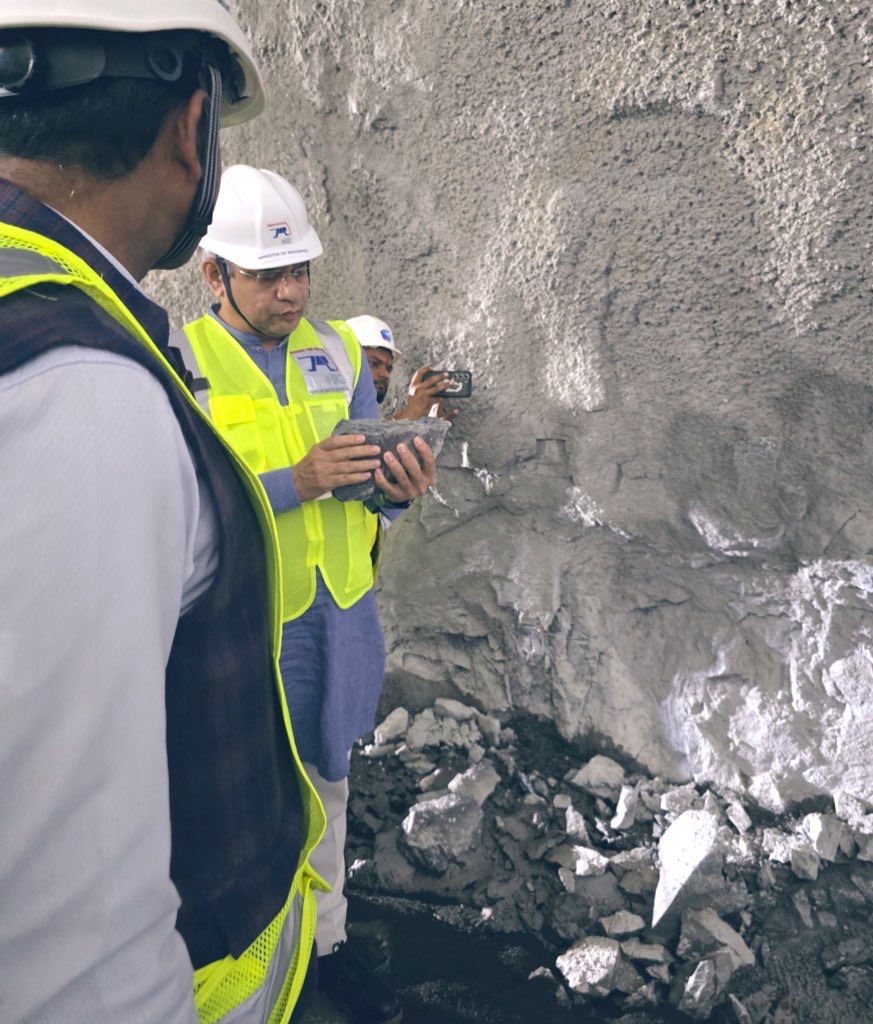
High-strength M70 grade concrete is being used to ensure superior structural integrity and long-term durability. The casting and stacking yard, covering an area of 11.17 Ha in Mahape, Thane district, Maharashtra. The yard will feature nine sets of moulds, each containing ten pieces.
Other details:
- Arrangement for Steam Curing after casting of segments. Final curing with curing compound.
- Quantity of Steel reinforcement in each ring: 4.368 MT.
- Quantity of concrete in each ring: 39.6 cum.
- Use of GFRP (Glass Fibre Reinforcement Polymer) bars to control cracking at edge.
- Batching Plant in Yard: 3 in Nos. Each having capacity: 69 cum/hrs.
- State of Art QA-QC lab at Yard having facilities to check durability parameter.
The yard is equipped with various cranes, gantries, and machines to automate and mechanize the casting operations, ensuring high-quality assurance during the casting and stacking of the segments. Additionally, the facility will include casting sheds, a stacking area, a batching plant, and a steam curing area.